What are those 3 most important things about a boiler? Water! Right Again! How can you tell where it is at? Peer through the looking glass although it is more commonly known as the water glass, sight glass or gauge glass.
The 3-dimensional chess continues with placing the water glasses on the backhead of the boiler. The board clamped in place served not only as a way to locate both FRA-required water glasses correctly but to facilitate checking for enough clearance around and under the other appurtenances already in place.

The metal plate clamped to the backhead serves as a nice flat baseplate for the magnetic based drill used to drill the holes for the appurtenances and studs.
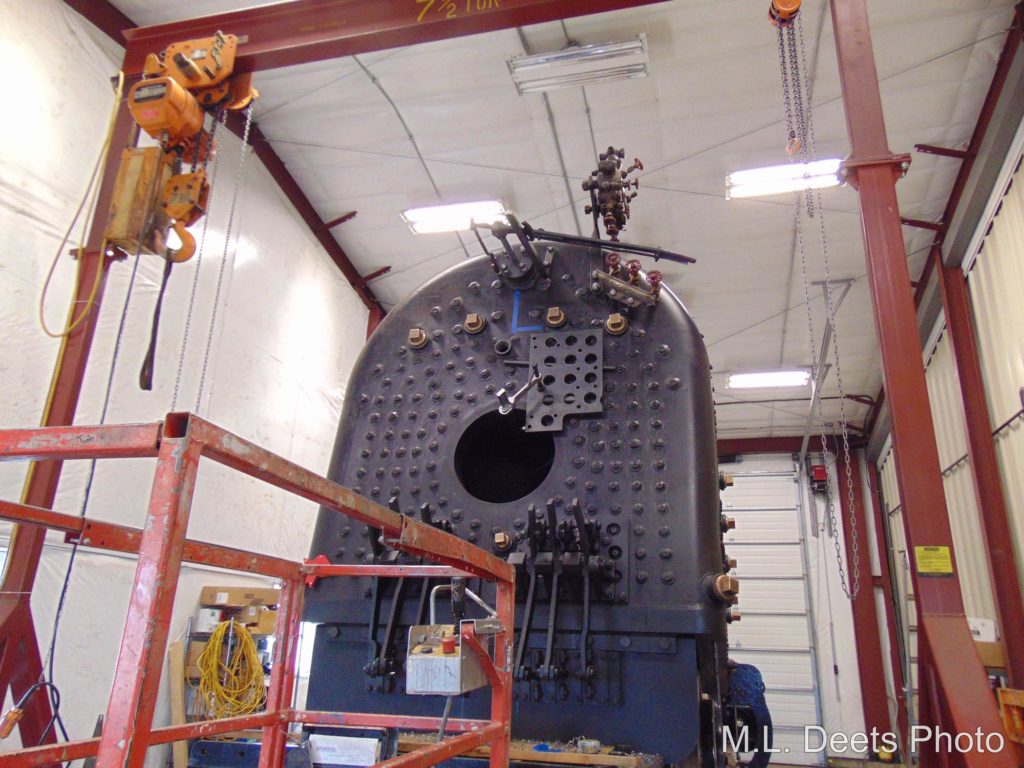
The plate is lined up for drilling of the hole for the first glass. The result is seen here. And like the bottom try-cock the lowest indication of the water glass is 4” above the highest point of the crownsheet per C&NW practice.
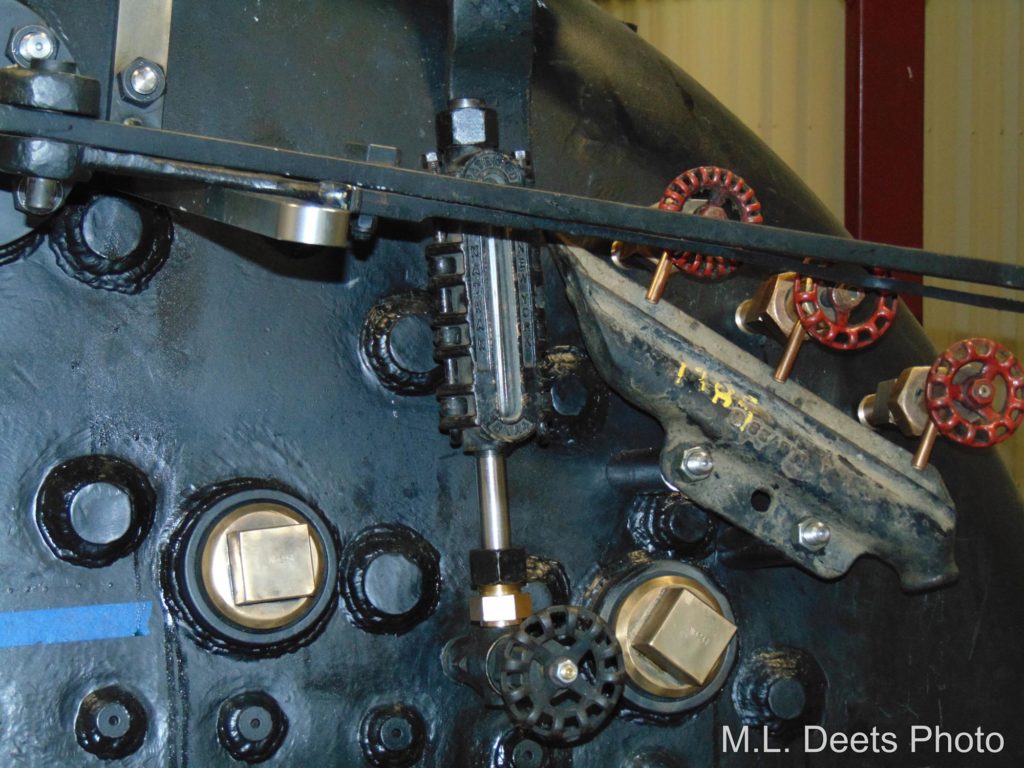
The plate was then moved to the fireman’s side where the single glass had been mounted on the original boiler and X marks the spot.
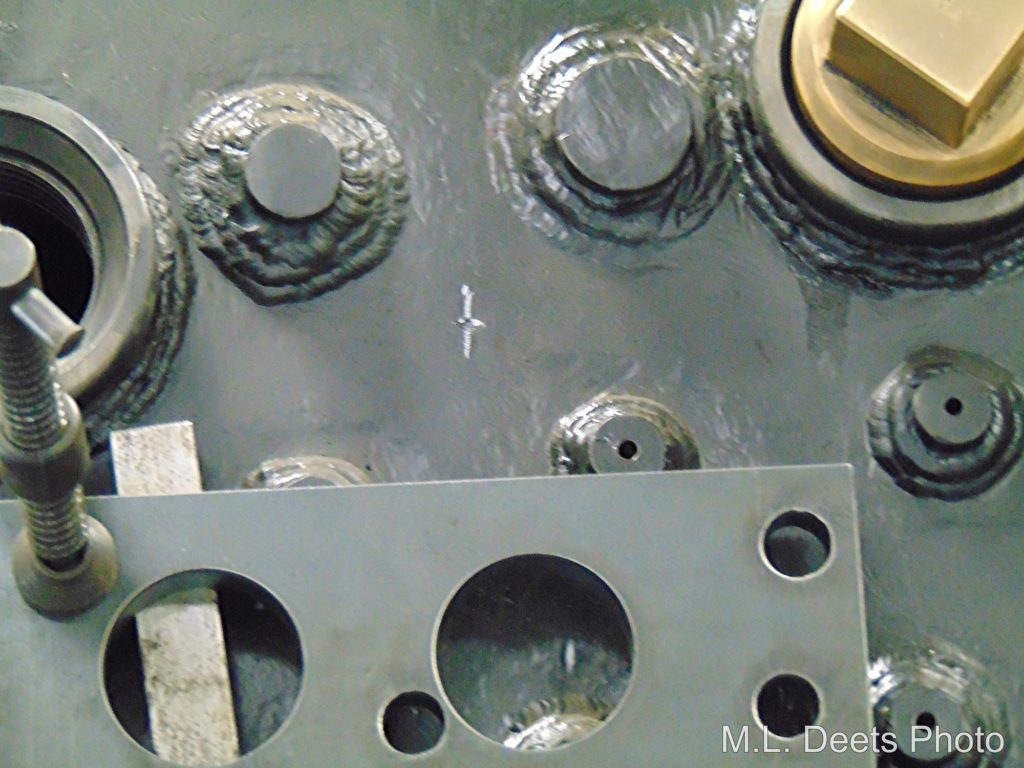
After drilling and tapping in the threads the second glass is seen here.
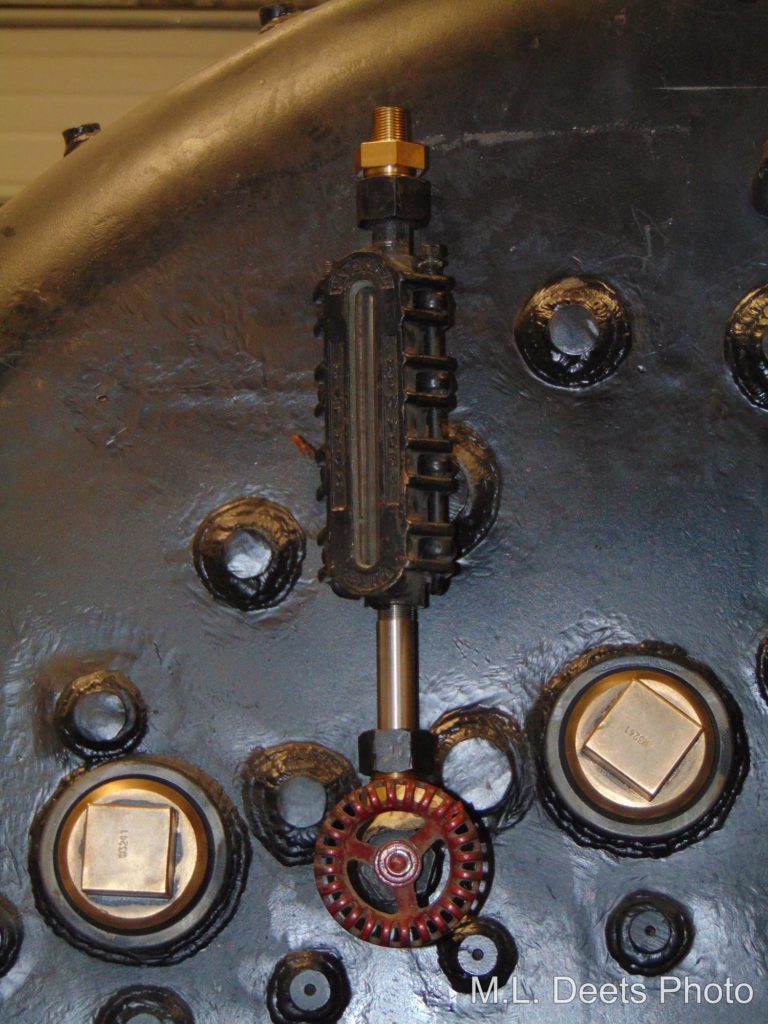
With both glasses mounted the backhead is looking more like a locomotive all the time.
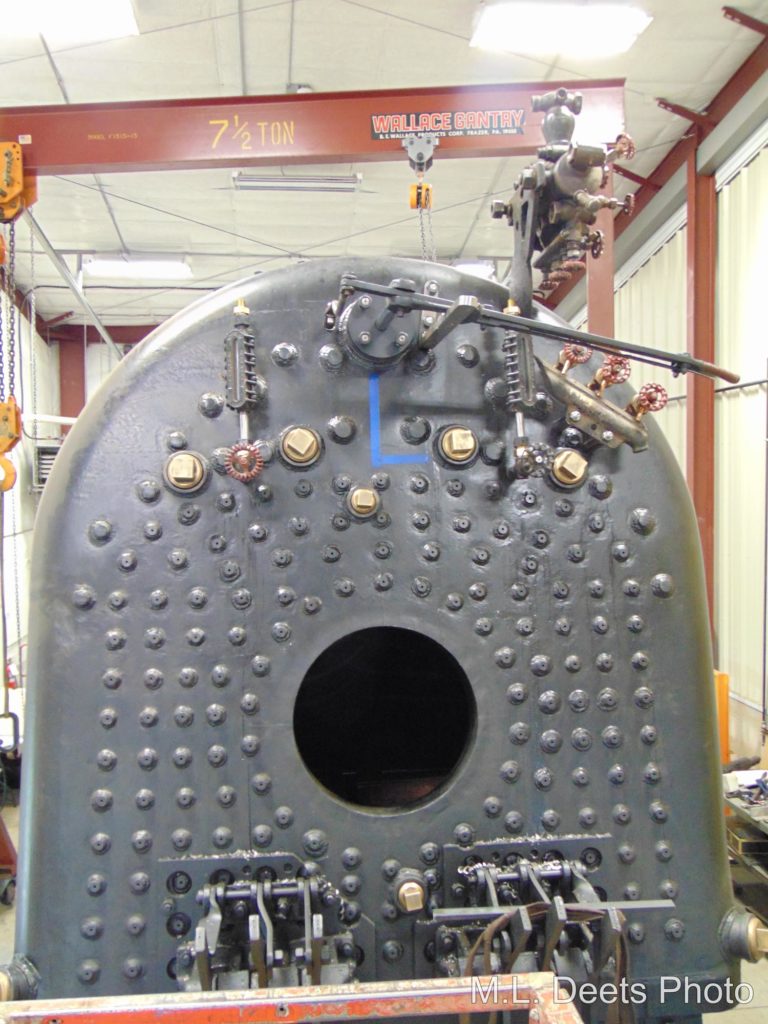
A volunteer session is being held on September 17 and 18 to work on the the C&NW #1385 locomotive tender. Tasks planned include filling the tender with water to check the truck spring compression and making any necessary adjustments. Additional work planned includes brake pipe fabrication. Persons with experience heating/bending pipe are highly encouraged to participate in this session. If there is sufficient help, other tasks in the Engine House will be tackled. Sign up by contacting project lead Ed Ripp or using the form on our Volunteering page.