During the last week of January Continental Fabricators began installation of the 1385’s backhead diagonal braces. The backhead is the end of the boiler located within the cab and is a large, flat plate or sheet of steel that has been flanged and then welded to the wrapper sheet. Flanging is the process of very carefully curling the edges of a sheet to meet the next piece it will be mated to. The flanging process has been covered in previous update posts.
Much of the boiler is round, a naturally strong shape. With areas that are flat or nearly flat the forces of nature (including steam pressure) are constantly trying to force them round and thus they require support or “staying”. Staybolts, or “stays” and braces are thus used to reinforce the area and prevent the backhead as well as the other flat areas from bowing outward when the boiler is under pressure.
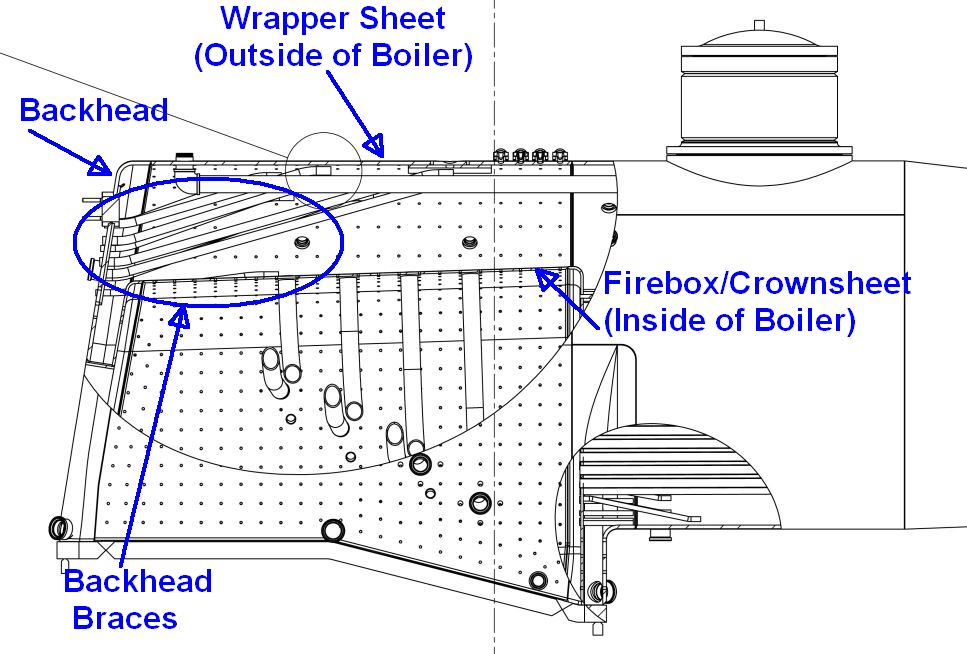
While installing these braces, crews at Continental Fabricators flipped the wrapper sheet/backhead assembly upside-down to facilitate easier working conditions. The first photo below shows the assembly as of the last week of January 2019 as the braces are being fitted and tack welded in place. The tack welds are just enough to hold the braces in place so this assembly can be righted and lowered onto the firebox/mud ring assembly to check for proper clearance between the braces and the firebox. Once Continental is satisfied with the fit-up between the pieces the wrapper assembly will once again be pulled off the firebox, inverted and the braces will receive the final welds.
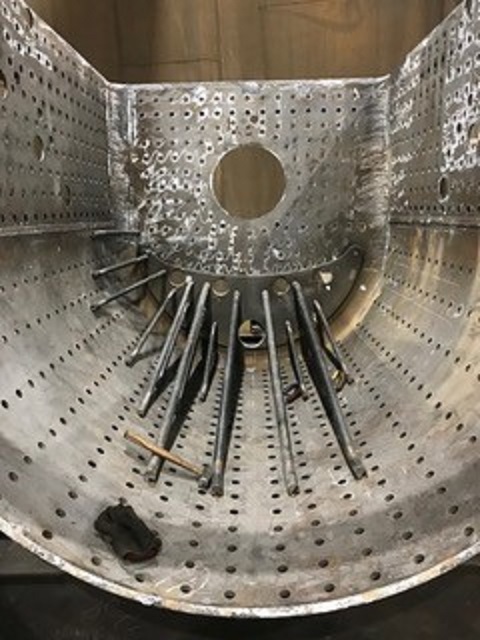
Much of the backhead will be supported via staybolts connected between it and the firebox door sheet. The pictured diagonal braces are used to support the part of the backhead that does not line up with the door sheet and is instead connected to the wrapper sheet for support. This picture was taken during the last week of Jan. 2019. Photo courtesy Continental Fabricators.
A few days later during this the first full week of February, Continental’s crews had flipped the backhead/wrapper sheet assembly right-side-up again and placed it over top the firebox/mud ring assembly. The purpose of doing this is to test fit for any contact between the backhead braces and the firebox crown sheet before final welding of the braces and before the wrapper sheet/backhead assembly is welded to the firebox/mud ring assembly. Once the two assemblies become one the installation of the staybolts can begin.
-
-
Test fitting the wrapper for proper clearance before completing backhead stay installation. Photo courtesy Continental Fabricators.
-
-
This photo was taken from the front of the firebox looking toward the backhead. It shows the steam/water space between the firebox/crownsheet and the wrapper sheet. Photo courtesy Continental Fabricators.